2, rue de la Ternière
Avrille Cedex FRANCE
- 150 million rectified pins designed per year
- Co-designer of custom fasteners for 100 years and manufacturer of standard products: iso 8734 or din 6325
- From Ø1.5 to Ø25 and from 8 mm to 100 mm
- Steel (free cutting, stamping, carbon, alloyed...), Stainless Steel (CNF or CND) Aluminum, Brass, etc.
They are often used in applications where fixing accuracy is essential, such as in machine tools, measuring equipment, and medical instruments.
Rectified cylindrical pin - din 6325 - iso 8734
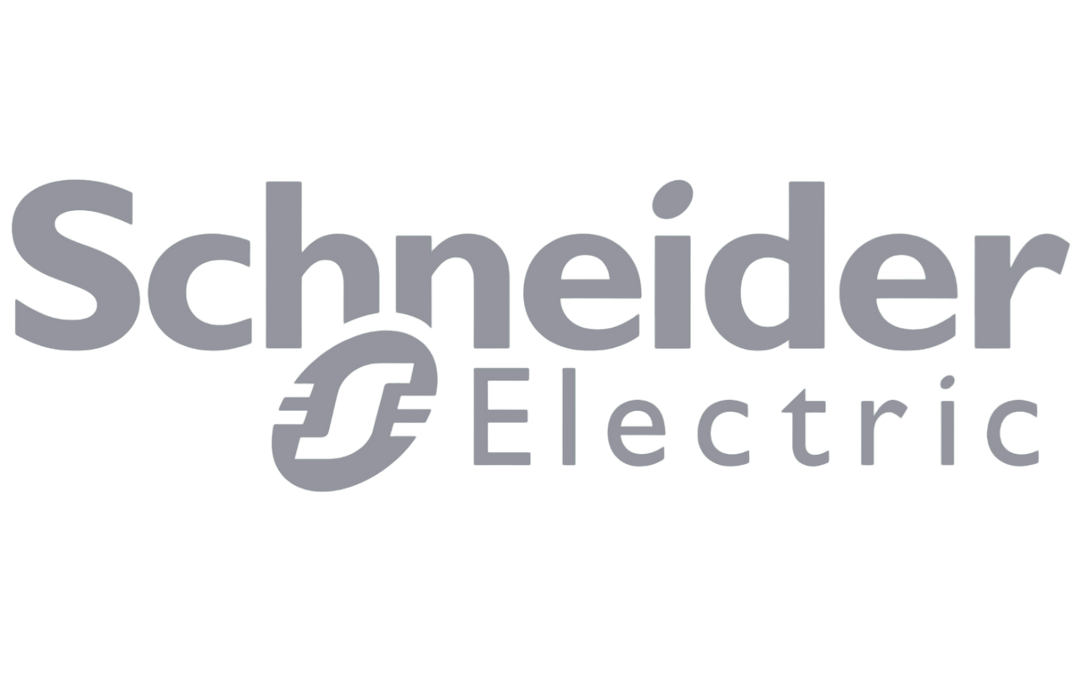
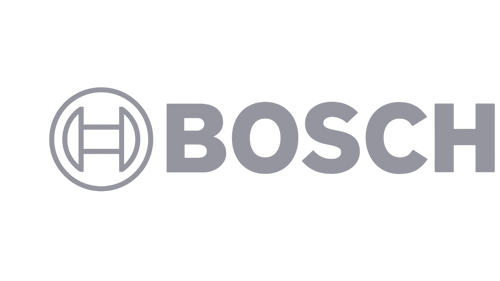
Rectified cylindrical pin - din 6325 - iso 8734
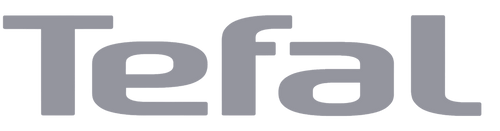
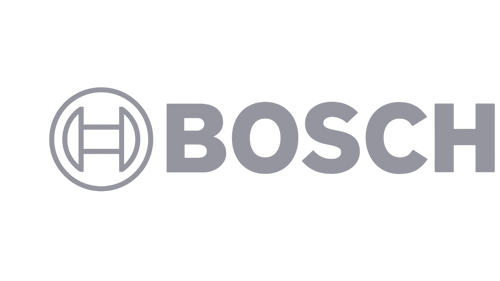
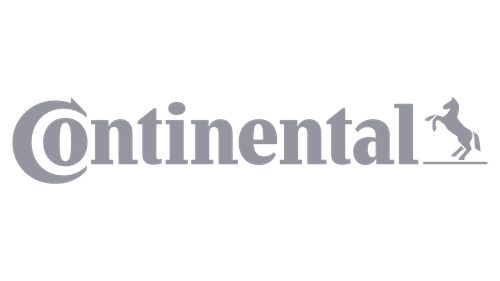
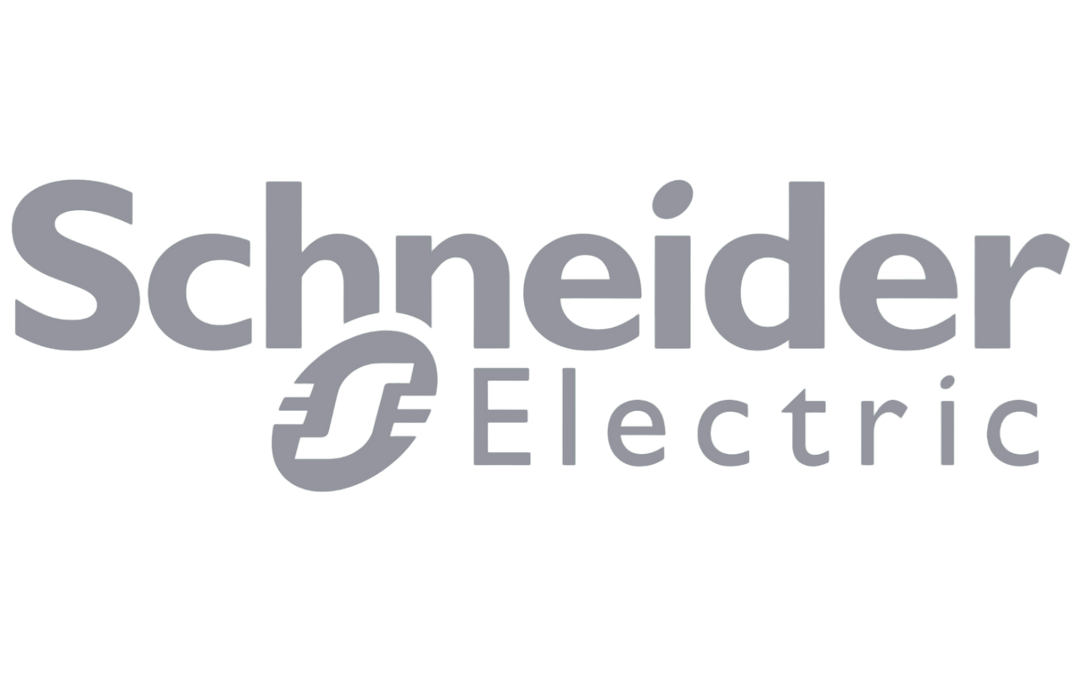
- Feasibility control using the FMEA tool, which is used to analyze failure modes, their effects and their criticality.
- Manufacture of initial samples in medium series, and validation of production with PPAP according to the IATF 16949 standard.
- Development of detailed production processes according to the APQP quality process
- Collection and analysis of production data to identify trends and variations. 3PPM in 2023.
The advantages of LGC Industries manufacturing
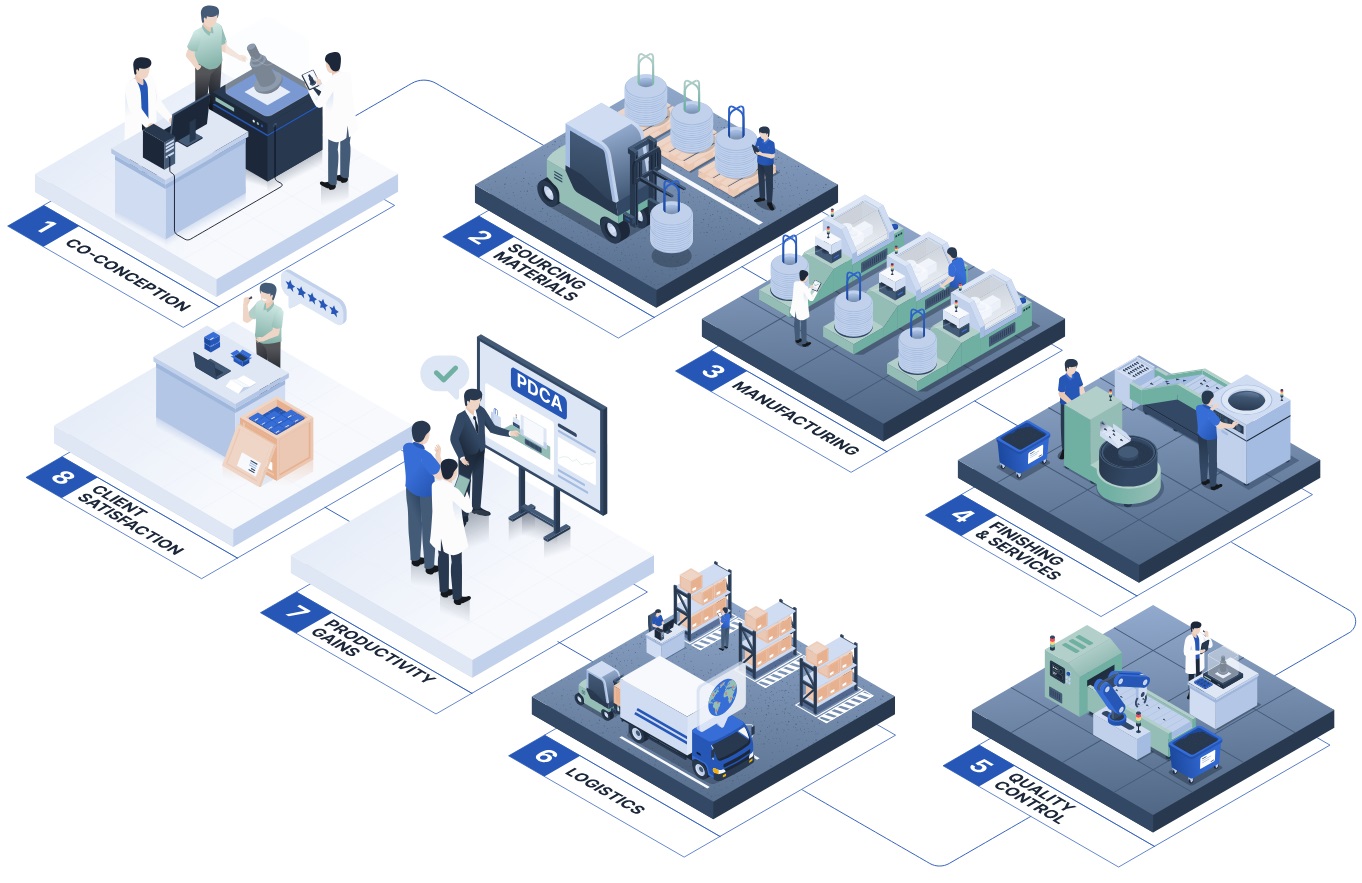
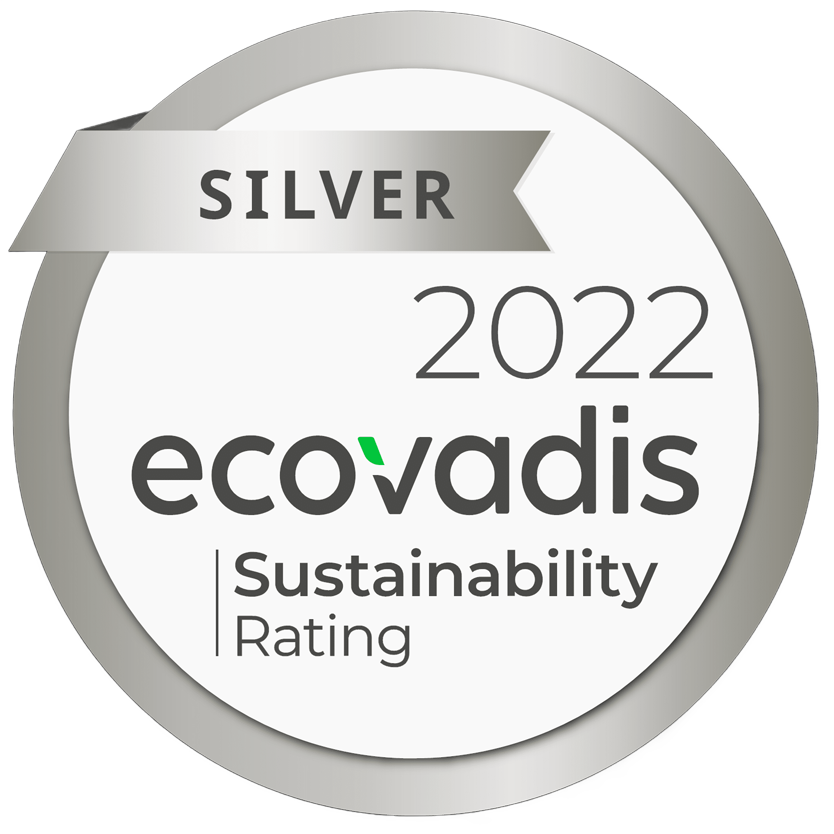
.png)

.png)


- 24 Multi-spindle lathes
- 45 Spins Escomatic
- 42 Fluting machines
- 8 Plunge and thread grinding machines
Learn more about the technical characteristics of our products
Discover other products
What is a rectified part?
A rectified part is a part that has undergone a finishing machining step called “grinding”, the treatment consists in removing material from the part using a grinding wheel in order to obtain the desired size and shape.
A rectified part is synonymous with precision because a rectified part is used in cases where tolerances and requirements are strict.
It is the wheel that comes into friction with the cylindrical pin, it is a disk or a band of abrasive material by:
- Corundum: capable of machining a wide variety of materials including plastic
- Diamond: used when it is necessary to machine very hard materials such as ceramics or hardened steels.
- Silicon carbide: used for hard materials such as steels.
At LGC, we can find different types of grinding wheels, each of which has its own specificities in grinding:
- Cylindrical grinding wheel: for classic cylindrical surfaces, for example for a cylindrical pin.
- Conical wheels: for conical surfaces, for example for a conical pin.
- Flat grinding wheel: for flat surfaces
The rectified cylindrical pin can be of any shape but there are standards to define standard pins. As far as the rectified cylindrical pin is concerned, there are the standards din 6325, iso 8734 and din 7.
What is a rectified cylindrical pin?
La rectified cylindrical pin Is a cylindrical pin whom has been subjected to a grinding process, which allows it to meet customer requirements and to correspond to din 6325, iso 8734 and din 7 standards.
Since this pin is used in very specific sectors of activity with very strict requirements, the pin is ground to the nearest micron.
For example, we can find a rectified cylindrical pin to meet the needs of different fields of application:
- On machine tools
- Measuring equipment
- Medical instruments.
How is an LGC ground pin made?
The LGC method for manufacturing a rectified cylindrical pin is similar to the manufacture of other pins since the basic steps are the same:
- 1st step: As for All the pins, the first step consists in cutting the bars of raw material, generally for the case of a rectified cylindrical pin, steel is used.
- The second step is a CNC machining process called bar turning. This is part of the turning family and consists in rotating the material by approaching the cutting tools until it comes into contact with the rotating material. Thin layers of material are successfully peeled off, which makes it possible to obtain the desired pin shape.
- Grinding is the third step, this is when the pin passes between the wheels in order to obtain a diameter accurate to the micron and a high quality surface finish. It is this process that makes it possible to obtain the standards din 6325, iso 8734 and din 7 for your rectified cylindrical pin.
- 4th step: LGC carries out a quality control at the end of the manufacturing process of your rectified cylindrical pin using high-tech measurement tools as well as the expertise of our employees (three-dimensional laboratory, 100% control machine, digital profile projector).
Once these 4 steps have been completed, we ship the parts to the customer by transport that requires as few CO2 emissions as possible.
What are the advantages of a rectified cylindrical pin?
When we read rectified cylindrical pin, we refer to the rectified cylindrical pin din 6325 or din 7 as well as to the rectified cylindrical pin iso 8734 or the cylindrical pin iso 2338.
What is the difference between these two pins?
These two pins are identical, the only thing that distinguishes them are the names of standards, the din 6325 cylindrical pin complies with the German standard while the iso 8734 cylindrical pin complies with the international one.
These may have different standard names but their benefits are the same:
- Precision: the precision offered by grinding ensures precise positioning of the pin in the assembly, ideal for axes of rotation or the positioning of cylinder heads for example.
- The resistance: after rectification, the rectified cylindrical pin considerably increases its resistance to wear, because its surface condition improves, this decreases friction which allows a reduction in maintenance needs.
- Comfort: the smooth surface offered by grinding with a ground cylindrical pin reduces noise and vibration during sliding or rotating movements.
- Aesthetics: the function of grinding is to improve the aesthetic appearance of a pin, this step offers a shiny and smooth surface.
- Standard product: Although LGC can meet your needs with a custom-made rectified cylindrical pin, the fact that this pin is recognized by the standards din 6325, iso 8734 and din 7, iso 2338 makes it a reference of choice.
What are the standards for rectified cylindrical pins?
The standards, whether German (din) or international (iso), define the criteria relating to the materials, dimensions and mechanical properties of cylindrical pins, thus ensuring their safety and reliability.
Here are the equivalences between din and iso standards for a rectified cylinder pin and a standard cylinder pin that we can design:
- din 6325 or iso 8734: rectified cylindrical pin
- din 7 or iso 2338: cylindrical pin