2, rue de la Ternière
Avrille Cedex FRANCE
- 35 million sockets designed per year
- Co-designer of custom fasteners for 100 years and manufacturer of standard products
- From M2.5 to M20 and from 6 mm to 22 mm
- Steel, stainless steel, brass, etc. (other materials are available on request).
Threaded sockets are cylindrical fixing means designed with an internal thread. They allow the assembly and fixing of parts with better resistance to tearing. These parts can also be overmolded.
Threaded socket - threaded cylindrical spacer
Threaded socket - threaded cylindrical spacer
- Feasibility control using the FMEA tool, which is used to analyze failure modes, their effects and their criticality.
- Manufacture of initial samples in medium series, and validation of production with PPAP according to the IATF 16949 standard.
- Development of detailed production processes according to the APQP quality process
- Collection and analysis of production data to identify trends and variations. 3PPM in 2023.
The advantages of LGC Industries manufacturing
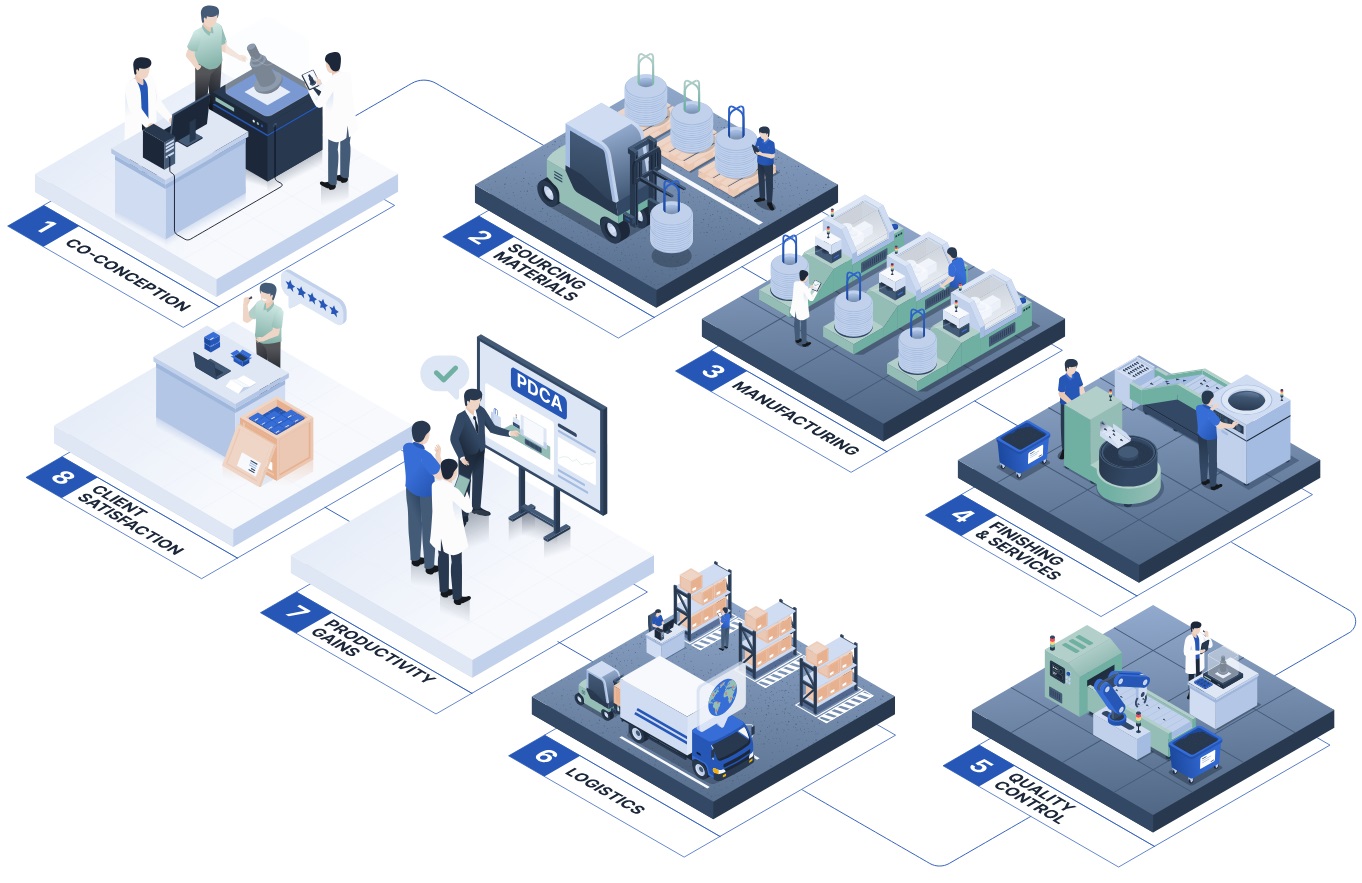
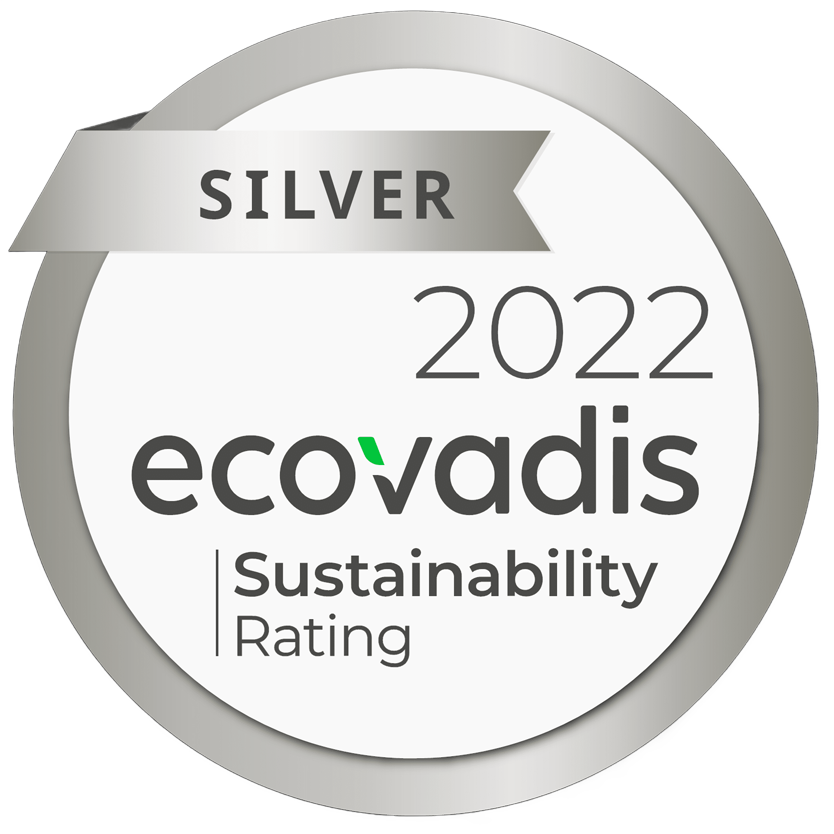
.png)

.png)


- 24 Multi-spindle lathes
- 45 Spins Escomatic
- 42 Fluting machines
- 8 Plunge and thread grinding machines
Learn more about the technical characteristics of our products
Discover other products
The threaded socket: assembly and fixing in one piece
Threaded sockets are essential elements in ensuring a solid and durable attachment of your parts. Thanks to their cylindrical design with an internal thread, they offer excellent pull-out resistance.
You can screw and unscrew them at will, which makes it much easier to assemble and disassemble your assemblies.
At LGC, we understand the importance of designing tailor-made solutions to meet your specific needs. This is why we support you throughout the process, offering prototyping, measurement and pull-out services. In addition, our expertise allows us to help you industrialize your project by offering you effective installation and assembly solutions.
How is an LGC threaded socket made?
From the material to the threaded socket
The manufacturing process for threaded sockets begins with steps similar to those of threaded inserts and self-tapping sockets.
The first step is to prepare the raw material coil.
Then, the part is deformed when cold, which improves the elastic strength of the material.
The second step is to cut the raw material tube in a suitable machine.
The tube is cut to the desired length. It is possible to add chamfers or finishes to the material.
Then, the part goes through a grinding stage. A roller presses the parts against a grinding wheel rotating at high speed. It is thanks to the abrasion of the grinding wheel that the diameter of the part is modified to reach tolerances of a few microns (~5-6 μm).
Finally, make way for tapping! A rotating tap will pass inside the part to give it the appropriate internal thread.
What are the advantages of a threaded socket?
- Reinforcement in soft materials: the threaded socket reinforces fasteners in soft materials, offering increased strength for fasteners with screws and bolts. This is particularly useful in assemblies subject to significant loads.
- Increased lifespan: thanks to its ability to provide a stronger thread, the threaded socket extends the life of the assembly by minimizing the wear of the thread over time.
- Reduced risk of tearing: these spacers reduce the risk of taps being pulled out, ensuring stable fastening even under conditions where loads may vary.
- Ease of repair: In the event of damaged tapping, a tapped socket provides an effective repair option, eliminating the need to replace expensive components.
- Application in demanding environments: the threaded socket withstands demanding environments well, offering a reliable solution even in conditions where other fastening methods could fail.
Would you like to learn more about the design of our sockets?
Go to our dedicated article: Everything you need to know about LGC sockets