2, rue de la Ternière
Avrille Cedex FRANCE
- 5 million new designs per year
- Co-designer of special fixings on drawings for 100 years
- IATF 16948, ISO 9001, Q1 Ford.
- We can produce numerous assembled, rectified, fluted and turned products
LGC Industries offers custom made special fasteners designed in collaboration with our customers to meet their specific fastening requirements. Our custom parts are manufactured according to the highest quality standards to ensure their durability and reliability.
Special mechanical part - Screw-cutting and precision machining
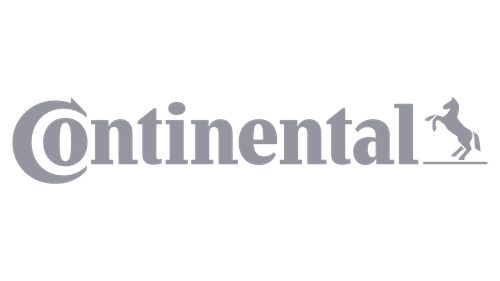
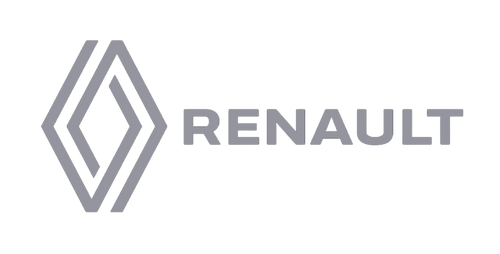
Special mechanical part - Screw-cutting and precision machining
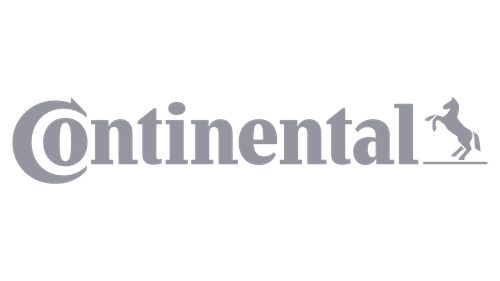
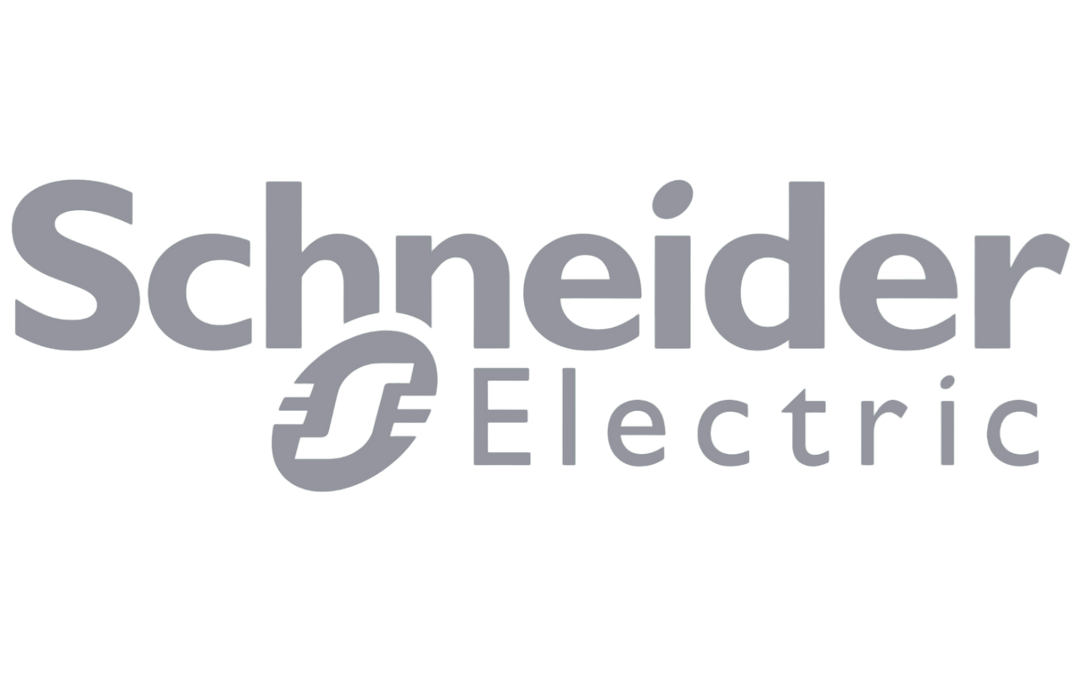
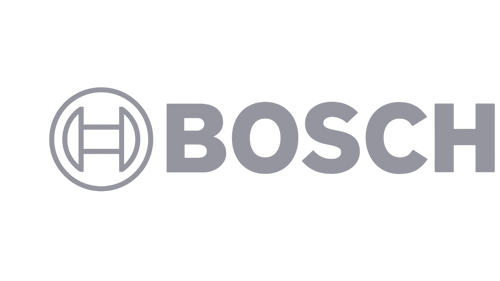
- Feasibility control using the FMEA tool, which is used to analyze failure modes, their effects and their criticality.
- Manufacture of initial samples in medium series, and validation of production with PPAP according to the IATF 16949 standard.
- Development of detailed production processes according to the APQP quality process
- Collection and analysis of production data to identify trends and variations. 3PPM in 2023.
The advantages of LGC Industries manufacturing
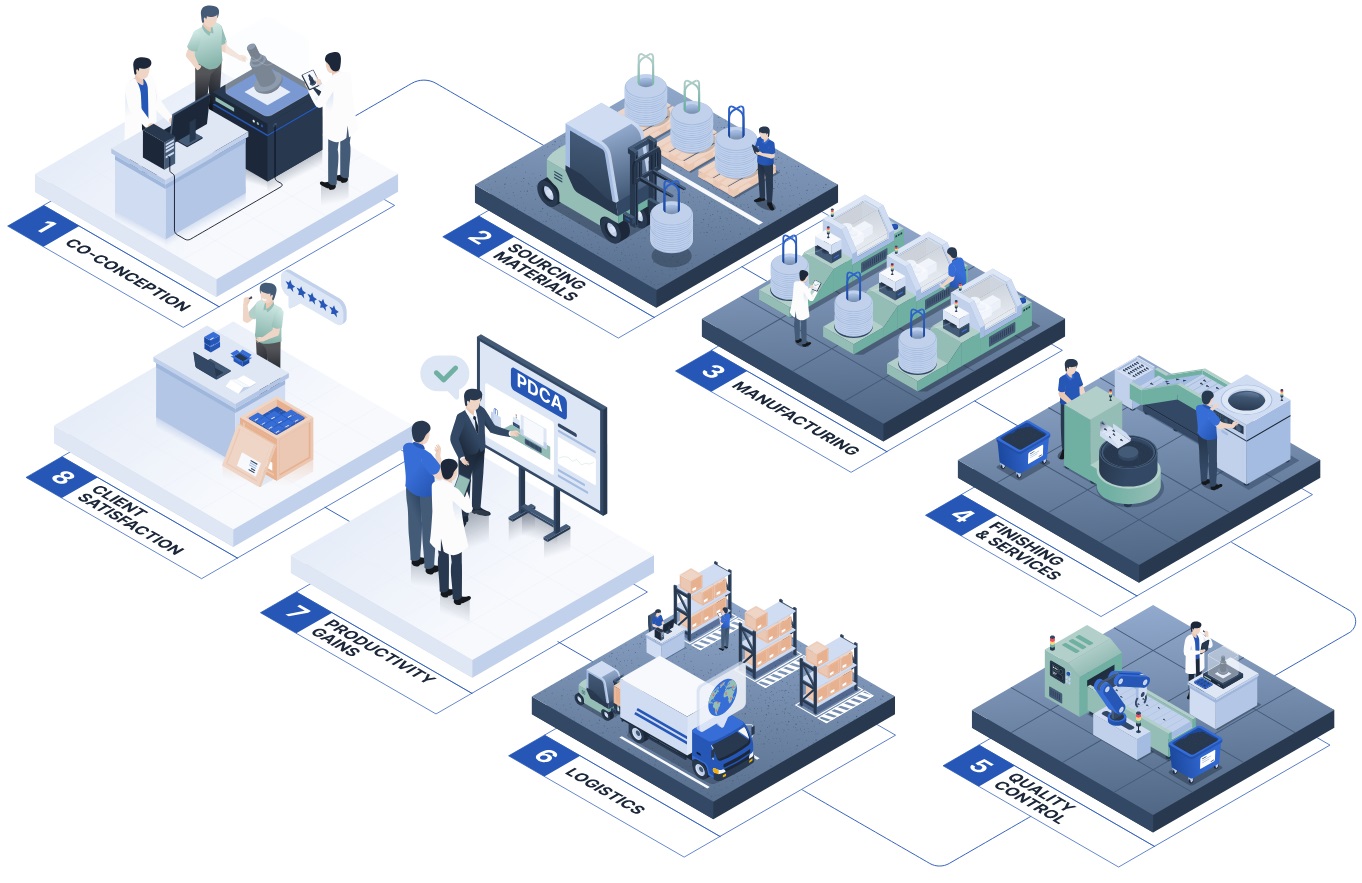
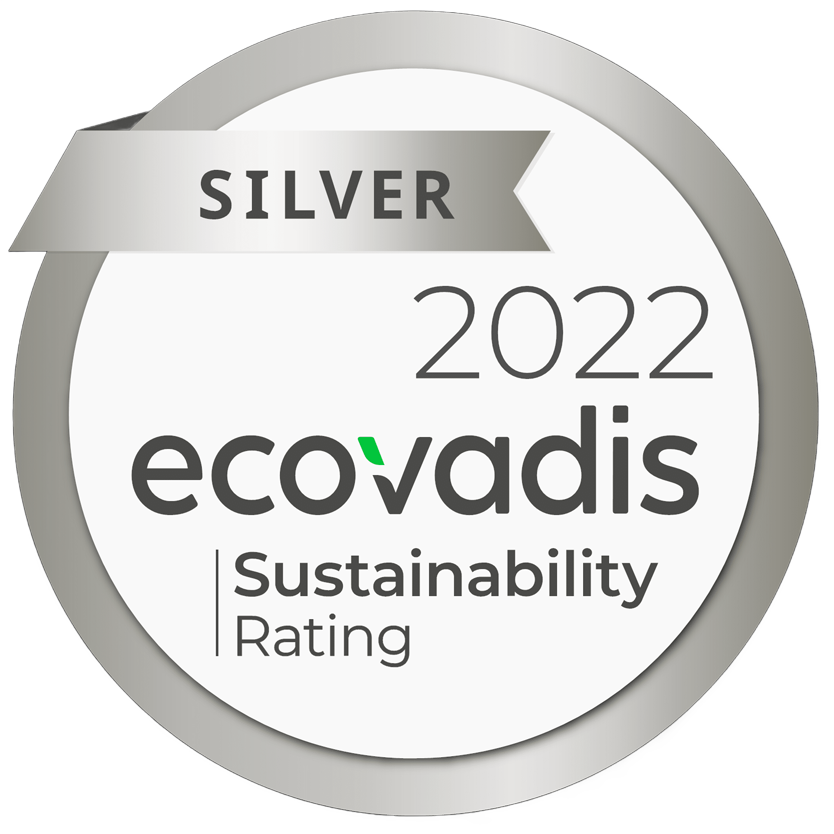
.png)

.png)


- 24 Multi-spindle lathes
- 45 Spins Escomatic
- 42 Fluting machines
- 8 Plunge and thread grinding machines
Learn more about the technical characteristics of our products
Discover other products
Precision turning and machining: from the raw material to the mechanical part of your dreams
The machining of mechanical parts is a manufacturing process by selective removal of material in order to transform a raw part into a special part corresponding to very specific dimensions and shapes.
There are various machining processes, at LGC we use CNC machining processes (numerical control machining) such as:
- The shooting
- Milling
- The drilling
- The decolleting...
Decolletage, a cutting-edge machining process that has been at the heart of our industry since its inception in the 18th century. Over time, it has evolved into modern bar turning thanks to the introduction of increasingly efficient and accurate CNC machining machines.
Today, the decolleting has become an essential process in the creation of precision mechanical parts that can be found in many advanced sectors requiring high quality parts.
- Aeronautics
- Automobil
- Electronic...
Bar turning is the ideal solution for obtaining special mechanical parts with precise shapes and flawless finishes.
At LGC Industries, we are proud of our expertise in bar turning, which we have integrated into the heart of the co-design of special mechanical parts for over 80 years.
Our commitment to excellence allows us to consistently exceed the expectations of our customers.
In addition, we are investing in new CNC machining machines in order to remain at the forefront of innovation and to guarantee ever more efficient results.
The different techniques for machining custom mechanical parts
The turning and machining of your mechanical parts are made possible thanks to our industrial facilities specialized in the design and production of parts by removing material.
Industrial installations that result in A machine park recent composed of numerous CNC machining machines:
- 24 multi-spindle CNC lathes
- 45 escomatic CNC lathes
- 42 fluting machines
- 8 plunge and thread grinding machines
- 2 cold forming machines
- 3 automatic packaging lines
- 6 optical sorting and metrology machines
- 2 robotic assembly lines
- 1 vibratory finishing and polishing unit
Machining and bar turning at the heart of co-design
At LGC Industries, we are specialists in the design and manufacture of mechanical parts and special fasteners to drawings.
Our aim is to meet your specific fastening requirements by working with you throughout the process.
We strongly believe in co-design with our customers.
We understand that each project is unique, so we work closely with you to develop and manufacture custom mechanical parts that will perfectly meet your needs in terms of dimensions, materials and performance.
Quality is at the heart of our approach.
All of our custom-made special parts are manufactured according to the highest quality standards to ensure their durability and reliability.
- ISO 9001
- ISO 14001
- IATF 16948
We make it a point of honor to provide you with high quality products.
As an environmentally responsible company, we also attach great importance to eco-design of our special pieces on plan.
We are committed to minimizing our environmental impact by using recyclable and sustainable materials as much as possible. In addition, we are implementing measures to reduce production waste in order to preserve our planet for future generations.